Picture this: You’re fixing a cracked kayak, and you’ve got two pieces of plastic that need to bond like they were never apart. You grab a heat gun, some rods, and go to work—only to end up with a warped, lumpy mess. Been there? I have too. That’s when I realized not all plastic welding is the same.
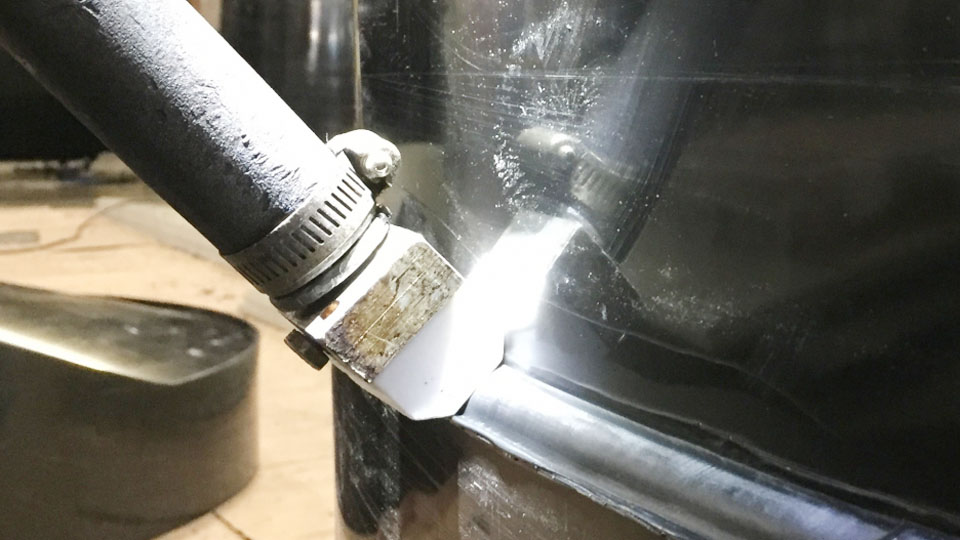
Image by cy-bo
I’ve tried every method under the sun, from backyard fixes to factory-grade techniques. Let me walk you through the different types of plastic welding, their pros and cons, and how to pick the best one for your project.
What Is Plastic Welding?
Plastic welding is like gluing, but better. Instead of adhesives, it uses heat, friction, or solvents to melt plastic pieces so they fuse together. The result? A bond that’s often as strong as the original material.
It’s used everywhere—car bumpers, plumbing pipes, medical devices, even toys. But here’s the catch: Plastics aren’t all the same. Some melt easily, others need precise heat control, and a few require zero heat at all. Let’s break down the methods.
Hot Gas Welding: The DIY Favorite
Hot gas welding is the “soldering iron” of plastic repair. You use a heat gun (or specialized welder) to blow hot air onto the plastic and a filler rod made of the same material. The heat melts both the rod and the base plastic, creating a seamless bond.
Best For: Thick plastics like PVC, HDPE, or polyethylene. Think kayaks, fuel tanks, or outdoor furniture.
Pros: Affordable, portable, great for large or irregular shapes.
Cons: Requires skill to avoid burning the plastic. Not ideal for thin materials.
My tip: Practice on scrap plastic first. Hold the gun at a 45-degree angle and keep the nozzle moving to spread heat evenly.
Ultrasonic Welding: Speed and Precision
Ultrasonic welding uses high-frequency vibrations (like a mini earthquake) to generate heat at the joint. The plastic molecules rub together, melt, and fuse in seconds. No filler needed.
Best For: Small, intricate parts—think car sensors, medical devices, or phone cases.
Pros: Lightning-fast (1–5 seconds per weld), no consumables, repeatable results.
Cons: Expensive equipment. Works best with thermoplastics like ABS or nylon.
I once watched a factory weld 500 syringe caps an hour with this method. Mind-blowing efficiency!
Vibration Welding: Big Parts, Big Results
Vibration welding is like ultrasonic’s beefy cousin. One piece of plastic is clamped down, the other vibrates rapidly under pressure. The friction melts the surfaces, which bond as they cool.
Best For: Automotive parts (dashboard panels, taillights), appliances, or large containers.
Pros: Strong, consistent welds on complex shapes. Handles thick materials.
Cons: Limited to parts that can withstand high vibration.
A friend used this to fix a cracked lawnmower housing. The weld held up for years!
Spin Welding: Circular Magic
Spin welding rotates one plastic piece against another at high speed. Friction heats the surfaces, and when you stop spinning, they fuse into a solid ring.
Best For: Round items like PVC pipes, bottle caps, or filters.
Pros: Simple, no filler, airtight seals.
Cons: Only works for circular joints.
I’ve repaired garden sprinklers this way. Just clamp, spin, and done!
Laser Welding: The High-Tech Option
Laser welding focuses a beam of light on the joint, melting the plastic precisely. A transparent layer is often placed over the weld to direct the laser’s energy.
Best For: Medical devices, electronics, or clear plastics where aesthetics matter.
Pros: No contact, zero debris, perfect for delicate parts.
Cons: Expensive machines. Limited to certain plastics (e.g., polycarbonate).
A local lab uses this for assembling IV drip chambers—sterile and flawless every time.
Solvent Welding: Chemical Bonding
Solvent welding isn’t technically welding—it uses chemicals (like acetone or MEK) to dissolve the plastic surfaces. When the solvent evaporates, the plastics merge into one piece.
Best For: PVC pipes, acrylic displays, or polystyrene models.
Pros: No heat or tools needed. Invisible joints.
Cons: Messy fumes. Works only with compatible plastics.
Safety note: Always wear gloves and work in a ventilated area. I learned this after a headache from gluing PVC without a mask!
Extrusion Welding: Heavy-Duty Repairs
Extrusion welding feeds molten plastic from a handheld extruder into the joint. It’s like a hot glue gun on steroids, ideal for thick or layered materials.
Best For: Industrial tanks, geomembranes, or HDPE liners.
Pros: Strong, deep penetration. Handles contaminated surfaces.
Cons: Bulky equipment. Steep learning curve.
I once patched a 500-gallon chemical tank with this method. Took patience, but it’s still leak-free!
Plastic Welding Methods Compared
Method | Best For | Equipment Cost | Skill Level | Strength |
---|---|---|---|---|
Hot Gas | Thick plastics, repairs | 50–50–500 | Moderate | Good |
Ultrasonic | Small, precise parts | $5,000+ | Low | Excellent |
Vibration | Automotive, large parts | $10,000+ | Moderate | Excellent |
Spin | Circular joints | 200–200–2,000 | Low | Good |
Laser | Delicate/clear plastics | $20,000+ | High | Very Good |
Solvent | PVC, acrylic | 10–10–50 | Low | Moderate |
Extrusion | Industrial tanks | $1,000+ | High | Excellent |
How to Choose the Right Plastic Welding Method
Ask yourself these questions:
- What type of plastic am I using? Check recycling codes (e.g., #2 HDPE, #5 PP).
- How strong does the weld need to be? Structural vs. cosmetic.
- What’s my budget? Hot gas is cheap; laser welding is an investment.
- Do I need portability? Solvent kits fit in a backpack; extrusion rigs need a truck.
For most DIYers, hot gas or solvent welding is a great start. Manufacturers lean toward ultrasonic or vibration.
Final Thoughts
Plastic welding opens up a world of repairs and creations—if you match the method to the material. Start small, master the basics, and gradually tackle tougher projects.
My first successful weld (a patched cooler lid) felt like a triumph. Yours will too. Remember, every cracked chair or broken pipe is a chance to learn. Keep experimenting, and soon you’ll weld like a pro.
FAQs About Plastic Welding
Can I weld any type of plastic?
No. Thermoplastics (like PVC, ABS) weld well; thermosets (epoxy, rubber) don’t melt and can’t be welded.
Which method is strongest?
Vibration or extrusion welding often creates the toughest bonds, but it depends on the plastic.
Is plastic welding safe?
Generally yes, but wear gloves, masks, and work in ventilated areas to avoid fumes.
Can I weld plastic with a soldering iron?
Yes, for small repairs. Use a low setting and compatible filler rod.
How do I know which solvent to use?
Check the plastic’s recycling code. PVC uses MEK, acrylic uses acetone.
Why did my weld crack after cooling?
Uneven heating or wrong filler material. Preheat the area and match the plastic type.
Can I weld wet or dirty plastic?
Dry and clean surfaces are best. Extrusion welding handles mild contamination.
What’s the cheapest way to start?
A $50 hot air gun and HDPE rods. Perfect for garden tools or outdoor gear.
With the right method in your toolkit, you’ll turn plastic problems into lasting solutions. Got a project in mind? Grab your gear and start melting! And if you’re stuck, drop me a line—I’ve got plenty of tips to share.