Stick welding, also known as Shielded Metal Arc Welding (SMAW), is a popular welding technique used in construction, fabrication, and repairs. It’s known for its simplicity and ability to work in various environments, even outdoors in windy or dirty conditions.
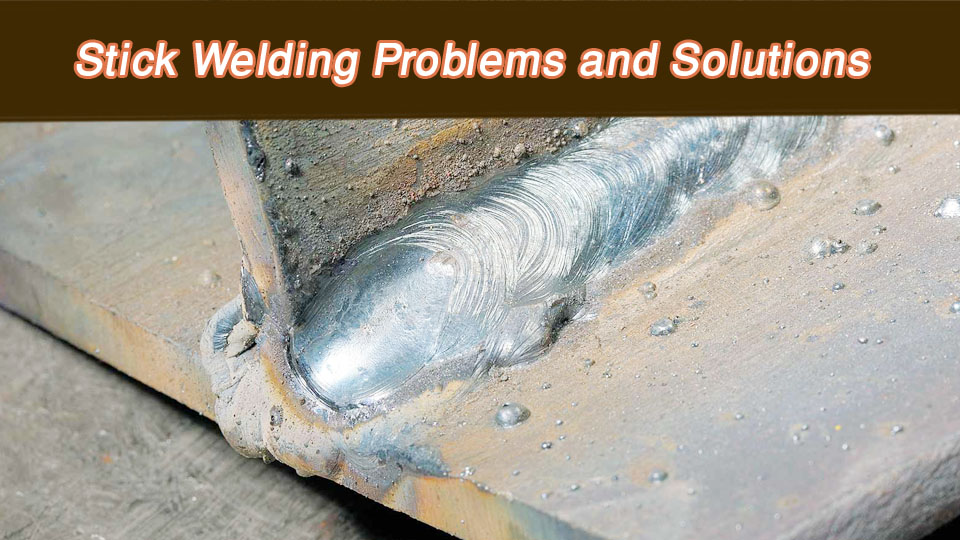
Image by twi-global
Like any welding method, stick welding comes with its own set of challenges. If you’ve faced issues like poor penetration, excessive spatter, or difficulty maintaining an arc, you’re not alone. There are practical solutions for each of these problems.
Electrode Sticking to the Workpiece
One of the most common frustrations in stick welding is the electrode sticking to the metal. This happens when the arc is not properly established or the electrode melts too quickly.
Causes:
- Low amperage setting
- Holding the electrode at the wrong angle
- Using a damp or old electrode
- Not striking the arc properly
Solutions:
- Increase the amperage slightly to allow better arc formation.
- Hold the electrode at a 15 to 30-degree angle to the workpiece.
- Use fresh, dry electrodes stored in a sealed container.
- Practice striking the arc by quickly tapping or scratching the electrode on the metal surface.
Excessive Spatter
Spatter refers to small molten metal droplets that scatter during welding. It can make the weld area messy and require extra cleanup.
Causes:
- High amperage setting
- Incorrect electrode angle
- Poor-quality or damp electrodes
- Arc length too long
Solutions:
- Reduce the amperage to a suitable level for the electrode type.
- Maintain a short arc length, keeping the electrode close to the workpiece.
- Use dry, high-quality electrodes.
- Adjust the electrode angle to keep it perpendicular to the work surface.
Poor Penetration
A weld with poor penetration lacks sufficient fusion between the base metal and the filler metal, making it weak.
Causes:
- Low amperage setting
- Moving the electrode too quickly
- Improper joint preparation
- Using an incorrect electrode
Solutions:
- Increase the amperage to allow for deeper penetration.
- Slow down the travel speed to let the molten pool form properly.
- Clean the base metal thoroughly and ensure a proper joint fit-up.
- Use an electrode suitable for the thickness of the metal being welded.
Porosity in Welds
Porosity refers to small holes or voids in the weld, which weaken the structure.
Causes:
- Moisture in the electrode or workpiece
- Contaminated base metal (rust, oil, paint, or dirt)
- Holding an excessively long arc
- Welding in windy conditions
Solutions:
- Keep electrodes dry and store them in a moisture-proof container.
- Clean the base metal thoroughly before welding.
- Maintain a consistent arc length to prevent excessive shielding gas loss.
- If welding outdoors, use windshields or relocate to a sheltered area.
Cracking in the Weld
Cracks in the weld can compromise the strength and durability of the welded structure.
Causes:
- Using the wrong electrode for the material
- Rapid cooling of the weld
- High residual stress in the metal
- Poor fusion between passes
Solutions:
- Choose the right electrode based on the material type.
- Preheat thick metals before welding and allow slow cooling.
- Use a multi-pass technique to distribute heat evenly.
- Ensure proper fusion between weld passes by overlapping beads.
Arc Blow
Arc blow occurs when the arc becomes erratic or deflects away from the intended path due to magnetic interference.
Causes:
- Welding near magnetic materials
- Improper ground clamp placement
- High current settings
Solutions:
- Change the ground clamp location to balance the magnetic field.
- Reduce amperage slightly to minimize the effect.
- Use AC current instead of DC to reduce arc blow.
Inconsistent Bead Appearance
A poorly formed weld bead looks uneven, weak, or inconsistent.
Causes:
- Unsteady hand movement
- Varying arc length
- Improper electrode angle
- Incorrect travel speed
Solutions:
- Practice steady hand movements to create a consistent bead.
- Keep the arc length uniform for stable welding.
- Maintain a proper electrode angle for better control.
- Adjust travel speed according to the thickness of the metal.
Common Stick Welding Problems and Solutions
Problem | Cause | Solution |
---|---|---|
Electrode sticking | Low amperage, wrong angle, damp electrodes | Increase amperage, adjust angle, use dry electrodes |
Excessive spatter | High amperage, poor arc length | Reduce amperage, maintain proper arc length |
Poor penetration | Low amperage, fast travel speed | Increase amperage, slow down travel |
Porosity | Moisture, contamination | Use dry electrodes, clean metal |
Cracking | Wrong electrode, rapid cooling | Use correct electrode, preheat thick metals |
Arc blow | Magnetic interference | Change ground clamp position, use AC current |
Inconsistent bead | Unsteady movement, wrong arc length | Practice steady hand control, keep arc length uniform |
Conclusion
Stick welding is a reliable and widely used welding process, but it does come with challenges. By understanding common problems and their solutions, you can significantly improve your welding results. The key is to maintain the right settings, practice good technique, and ensure clean working conditions.
If you’re a beginner or an experienced welder, troubleshooting these issues will help you produce stronger, more professional-looking welds.
Frequently Asked Questions
Why does my electrode keep sticking?
Your electrode may be sticking due to low amperage, a poor striking technique, or damp electrodes. Try increasing the amperage, striking the arc correctly, and using dry electrodes.
How do I reduce excessive spatter in stick welding?
Excessive spatter can be minimized by lowering the amperage, keeping a short arc length, and using high-quality electrodes.
What causes weak welds in stick welding?
Weak welds are often caused by poor penetration, improper electrode selection, or contamination. Use the correct amperage, choose the right electrode, and clean the base metal before welding.
Why do my welds have holes in them?
Holes in the weld, or porosity, occur due to moisture, dirt, or an excessively long arc. Keep your electrodes dry, clean the workpiece, and maintain a steady arc length.
Can I prevent cracking in my welds?
Yes, cracking can be prevented by selecting the right electrode, preheating thick metals, and ensuring a gradual cooling process after welding.
By mastering these troubleshooting techniques, you’ll be able to weld with more confidence and achieve professional-quality results every time.