Welding is an art and a science. It’s something I’ve dedicated years of my life to mastering, and I still find myself learning new things every day. One of the questions that often comes up—especially when working with advanced or mixed-metal projects—is: Can titanium be welded to steel? The short answer is: yes, but it’s complicated.
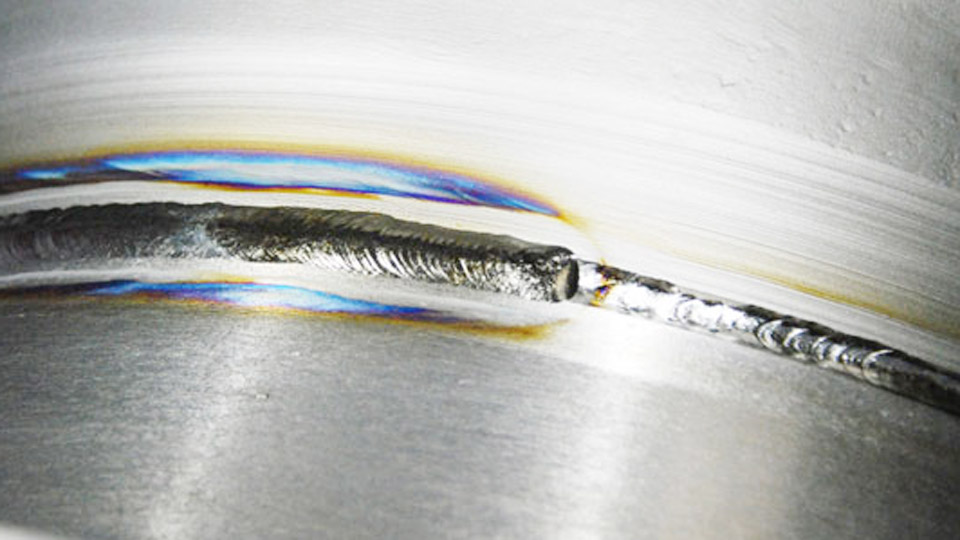
Photo by sureflowequipment
This isn’t like fusing two pieces of mild steel together. Titanium and steel are very different metals. Their physical properties, chemical behaviors, and even how they respond to heat are almost on opposite ends of the spectrum.
With the right technique, proper precautions, and a clear understanding of the challenges involved, it’s definitely possible.
Let me walk you through everything you need to know if you’re curious about, or even planning to weld titanium to steel.
Why Welding Titanium to Steel is So Challenging
The first thing I always tell folks is that this isn’t a beginner welding job. If you’re new to welding, you’ll want to get a lot more experience under your belt before tackling something like this. The biggest hurdle comes down to how titanium and steel react differently during the welding process.
Titanium is highly reactive at elevated temperatures. When exposed to oxygen, nitrogen, or hydrogen during welding, it forms brittle compounds that can completely ruin the weld. On the other hand, steel—especially carbon steel—doesn’t have the same kind of sensitivity, and it’s a lot more forgiving.
Let’s take a quick look at a few of the biggest differences between the two metals:
Property | Titanium | Steel |
---|---|---|
Melting Point | ~3,034°F (1,668°C) | ~2,500°F (1,370°C) (carbon steel) |
Thermal Conductivity | Low | Higher |
Reactivity | Very high (in molten state) | Lower |
Density | Lightweight | Heavier |
Expansion Rate | Low | Moderate |
Because of these differences, a direct fusion weld (where both metals are melted and joined together) often leads to brittle intermetallic compounds. These compounds are like the villains of metallurgy—they make the weld weak, prone to cracking, and just not structurally sound.
What Happens If You Try to Weld Them Directly?
I’ve experimented with direct fusion welding of titanium and steel in controlled environments, and let me tell you—it usually ends badly. When the two metals mix at the weld interface, they form titanium iron intermetallics like TiFe and TiFe₂. These compounds are incredibly hard but also very brittle.
So while the joint might look okay on the surface, it won’t hold up under stress. That’s a major problem if the part is going to see any real-world use.
If you’re curious or attempting this kind of weld out of necessity, you should know the standard welding processes won’t work directly. You’ll need to introduce something else between the two metals.
Dissimilar Metal Welding: What Actually Works
To successfully join titanium to steel, we often use a technique called dissimilar metal welding, which involves using a transition layer or intermediate material between the two metals.
Some of the most effective methods include:
- Explosion Welding
- Friction Welding
- Diffusion Bonding
- Bimetallic Transition Inserts
Each of these methods avoids forming those harmful brittle compounds by keeping titanium and steel from directly mixing. Let me break them down for you.
Explosion Welding
This might sound like something out of a science fiction movie, but explosion welding is a real and effective method. It uses a controlled detonation to slam two metals together at extremely high velocity.
The force of the explosion causes the atoms at the interface to bond, without melting either metal. That means no intermetallics and a solid bond.
I’ve seen this used to create bimetallic plates—sheets of steel and titanium joined together in a way that would be impossible with traditional welding. The downside? It’s not a DIY process. This is something done in highly controlled industrial environments.
Friction Welding
Another powerful method is friction welding, especially rotary friction welding.
In this process, one metal is spun rapidly against the other under pressure. The heat generated by friction softens the interface just enough for a solid-state bond to form—again, without melting.
This method works really well for cylindrical parts, like rods or tubes. It’s widely used in aerospace and automotive industries.
I’ve personally worked on projects where titanium drive shafts were friction-welded to steel flanges. The result was an incredibly strong, clean bond that could stand up to vibration and torque.
Diffusion Bonding
This technique involves pressing the two metals together at high temperatures for a long time, typically in a vacuum or inert atmosphere. The atoms slowly migrate across the boundary, forming a bond without melting.
It’s a slow process, but it allows for very precise and controlled joining. It’s mainly used in high-tech industries like aerospace or nuclear engineering, where even microscopic flaws are unacceptable.
While not common in everyday shops, it’s a fascinating example of how we can push the boundaries of welding science.
Bimetallic Transition Inserts
Now, here’s the method I recommend most often if someone needs to connect titanium to steel in a practical setting.
Bimetallic transition inserts are specially fabricated pieces that have titanium on one side and steel on the other, already joined together using one of the solid-state techniques above (like explosion welding). You can then weld your titanium component to the titanium side, and your steel part to the steel side—using standard welding methods.
I’ve used these inserts in several industrial builds, and they save a ton of hassle. Just be sure you know exactly what kind of insert you’re getting and that it’s rated for the application.
Protecting the Weld: The Role of Shielding Gases
Even when you’re welding on the titanium side, proper shielding is critical.
Titanium doesn’t forgive. The moment it hits air while hot, it oxidizes. That means you need 100% argon shielding—sometimes even trailing shields or glove boxes to protect the weld from start to finish.
I always tell people: if your titanium weld starts turning blue, purple, or worse—green or gray—it’s already contaminated. A clean titanium weld should be silver and shiny.
Steel isn’t as sensitive, but when you’re welding near a transition zone or using inserts, you still want clean gas coverage. It helps prevent oxidation at the interface, and every little bit counts when working with dissimilar metals.
Choosing the Right Filler Metal
If you’re doing any welding beyond using pre-bonded inserts, you might be wondering about filler metals.
Unfortunately, there’s no perfect one-size-fits-all filler for welding titanium directly to steel. Most attempts result in the same brittle intermetallics I talked about earlier.
That’s why filler metals are rarely used unless there’s an intermediate alloy in play. In many cases, copper or nickel-based alloys might be used in research or lab settings, but they aren’t practical for field work.
If you’re using bimetallic inserts, just match the filler to the base metal on each side—titanium filler (like ERTi-2 or ERTi-5) for titanium, and appropriate steel filler (like ER70S-2 or stainless filler) for the steel side.
Common Mistakes to Avoid
Let me spare you a few headaches by going over the most common mistakes I see folks make when trying to weld titanium to steel:
- Using standard TIG or MIG on both metals directly: It won’t hold. The weld will crack under stress.
- Skipping the shielding gas or using mixed gas blends: For titanium, only pure argon will do.
- Not cleaning the base metals properly: Any contamination, especially on titanium, can ruin the weld.
- Ignoring thermal expansion differences: Titanium and steel expand at different rates, which can lead to stress and cracking over time.
- Welding without transition materials: You’re just asking for failure.
Where is Titanium-to-Steel Welding Used?
You might be wondering, “Why even bother with such a difficult weld?”
It turns out, titanium-to-steel joints are used more often than you’d think—especially in industries like:
- Aerospace: Lightweight titanium components need to attach to stronger steel structures.
- Chemical processing: Titanium resists corrosion, so it’s often used where steel can’t survive.
- Marine applications: Saltwater is brutal on steel, but titanium stands up much better.
- Nuclear and defense: Where performance matters more than cost.
I’ve seen these types of joints in pressure vessels, pipe systems, shipbuilding, and advanced machinery.
My Final Thoughts on Welding Titanium to Steel
So, can titanium be welded to steel?
Yes—but only if you respect the science behind it. It’s not a job for shortcuts or guesswork. You need the right tools, techniques, and most importantly, a good understanding of how both metals behave.
I’ve worked on enough titanium-to-steel projects to know that patience and preparation make all the difference. If you’re fabricating parts for aerospace, marine, or just exploring new welding challenges, mastering this process can really elevate your skills.
Frequently Asked Questions
Can I weld titanium to stainless steel at home?
Technically yes, but I wouldn’t recommend it unless you have access to solid-state bonding inserts or specialized equipment. Direct welding will likely fail.
What filler rod should I use for titanium-to-steel welding?
There is no universal filler rod for directly joining titanium to steel. Use transition inserts and match the filler metal to each base metal separately.
Why does my titanium weld turn blue or purple?
That’s a sign of contamination—usually oxygen getting into the weld area. Use pure argon shielding and make sure the metal is clean and protected.
Is explosion welding safe?
Yes, when done in a controlled industrial environment by trained professionals. It’s not a method for home or small-shop welders.
Can I use MIG welding for titanium and steel?
MIG is not ideal for titanium at all. Titanium should be welded with TIG using pure argon shielding. Steel can be MIG welded, but not in a dissimilar metal joint like this.