Aluminum welding rods come in many different types, but the two most commonly used are 4043 and 5356. As someone who’s spent a lot of time in the world of welding, I know firsthand how easy it is to get confused by all the options out there.
When you’re choosing between 4043 and 5356 aluminum rods, it’s essential to understand the unique properties, applications, and benefits of each.
I’ll walk you through everything you need to know about these two popular alloys, helping you decide which one is best for your project.
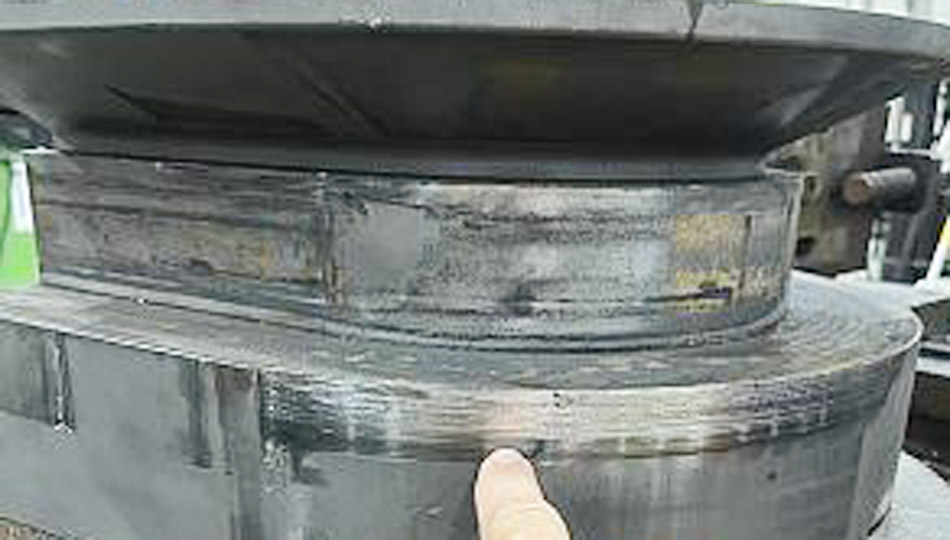
Image by thefabricator
Basics of Aluminum Welding Rods
Aluminum is a versatile and lightweight material used across various industries, from automotive and aerospace to construction and marine applications. One of the most crucial aspects of working with aluminum is selecting the right filler metal, especially when you’re welding. The right filler rod ensures that the weld is strong, durable, and resistant to the elements.
Two of the most commonly used aluminum welding rods are 4043 and 5356. Both are made from aluminum alloy, they have different compositions and properties that make them suitable for specific applications. As I’ve worked with these rods over the years, I’ve learned the ins and outs of both, and I’m excited to share that knowledge with you.
Composition of 4043 and 5356 Aluminum
Before diving into the differences, let’s take a closer look at the compositions of these two rods.
4043 Aluminum Filler Rod
The 4043 aluminum welding rod is primarily made of aluminum, but it also contains silicon as its alloying element. Silicon helps improve fluidity during the welding process, making it easier to work with. Here’s the general breakdown of the composition of 4043:
- Aluminum: 93.5%
- Silicon: 4.5%
- Iron: 0.3%
- Copper: 0.1%
- Magnesium: 0.05%
- Zinc: 0.1%
- Other Elements: Trace amounts of other metals
This composition makes 4043 a great choice for welding aluminum alloys that don’t contain a high level of magnesium, such as 6061, 3003, and 5052.
5356 Aluminum Filler Rod
The 5356 aluminum rod, on the other hand, is a stronger alloy due to the higher magnesium content. This rod contains about 5% magnesium, which significantly increases its strength and corrosion resistance. The composition of 5356 is as follows:
- Aluminum: 94.5%
- Magnesium: 5.0%
- Manganese: 0.3%
- Chromium: 0.1%
- Iron: 0.2%
- Silicon: 0.3%
The higher magnesium content makes the 5356 filler rod ideal for applications that require increased strength and resistance to corrosion, such as in the marine, automotive, and welding of high-strength aluminum alloys.
Comparing the Mechanical Properties
When selecting a welding rod, it’s crucial to consider the mechanical properties of the material. These properties determine how the weld will perform under stress and exposure to the environment.
Strength and Durability
4043
While 4043 is a relatively strong filler rod, its strength is lower than that of 5356. The 4043 rod is best suited for applications where moderate strength is required, such as light fabrication and repair work. It works well in projects where high tensile strength isn’t as critical.
5356
The 5356 aluminum welding rod is stronger, thanks to its higher magnesium content. This makes it a better choice for heavy-duty applications that require greater strength, such as welding in marine environments, pressure vessels, or the automotive industry. It can handle higher loads and is more resistant to wear and tear.
Corrosion Resistance
4043
One of the reasons that 4043 is often chosen for certain welding applications is its good resistance to corrosion, but it doesn’t perform as well as 5356 when exposed to harsh conditions. For example, 4043 is not the best option for marine environments, where exposure to saltwater is common.
5356
Due to the higher magnesium content, 5356 excels in environments where corrosion resistance is critical. It is widely used in marine environments, as it resists saltwater corrosion better than 4043. If you’re welding aluminum in areas exposed to moisture, 5356 is a superior choice.
Applications of 4043 and 5356 Aluminum Filler Rods
Both rods are versatile, but their unique properties make them better suited for different welding tasks.
Applications for 4043 Aluminum Filler Rod
4043 is often used in general-purpose applications and is a popular choice for repairs and welding of aluminum alloys that do not require extreme strength. Some of the most common applications include:
- Welding of aluminum alloys: It is ideal for alloys like 6061, 3003, and 5052.
- Repair work: 4043 is commonly used for repairs on aluminum castings, engines, and structures.
- Light fabrication: It’s great for general fabrication of aluminum parts, such as furniture and small components.
- Automotive repairs: It is frequently used in the repair of aluminum body panels, especially in older vehicles.
Applications for 5356 Aluminum Filler Rod
With its higher strength and resistance to corrosion, 5356 is typically used in more demanding applications. Here are some areas where 5356 excels:
- Marine applications: It’s used to weld aluminum boat hulls, docks, and other parts exposed to saltwater.
- Automotive industry: It is used for welding automotive parts, especially in vehicles requiring high strength, such as trailers and chassis.
- Pressure vessels: The increased strength and corrosion resistance make 5356 the perfect filler rod for welding pressure vessels, gas tanks, and heat exchangers.
- Welding high-strength alloys: It’s ideal for welding high-strength aluminum alloys like 5083, 5086, and 6061.
Weldability: 4043 vs 5356
When it comes to weldability, both rods are relatively easy to use, but there are differences in how they behave during the welding process.
4043
This rod is more forgiving than 5356, and it has excellent fluidity. This makes it easier to achieve smooth, clean welds. It’s also less prone to cracking in less-than-ideal conditions, making it a good choice for beginners and those doing occasional repairs.
5356
While 5356 is slightly harder to weld due to its higher magnesium content, it offers better results in terms of strength and durability. The higher magnesium can lead to more sensitivity to heat input and a higher risk of cracking, but if you follow proper welding techniques, it can produce strong, high-quality welds.
Choosing the Right Filler Rod: 4043 vs 5356
When deciding between 4043 and 5356, the best choice depends largely on your specific project requirements.
Factor | 4043 | 5356 |
---|---|---|
Strength | Moderate strength, suitable for general work. | High strength, ideal for demanding applications. |
Corrosion Resistance | Good resistance but less than 5356. | Excellent resistance to corrosion, especially in marine environments. |
Weldability | Easier to weld, good for beginners. | More challenging to weld but stronger and more durable. |
Applications | General repairs, light fabrication. | Marine, automotive, pressure vessels, high-strength alloys. |
Conclusion
Both 4043 and 5356 are excellent filler rods, but they are suited for different types of welding projects. After using both in various applications, I’ve learned that 4043 is the go-to option for general-purpose welding where strength isn’t the highest priority. It’s easier to work with and more forgiving, making it a good choice for beginners or repair work.
5356 offers superior strength and corrosion resistance, making it the ideal choice for demanding projects like marine welding, high-strength aluminum alloys, and situations where the weld will be exposed to harsh conditions.
Understanding the unique properties of each alloy is key to selecting the right one for your specific needs. By choosing the correct filler rod, you can ensure strong, durable welds that will stand the test of time.
Frequently Asked Questions (FAQs)
Can I use 4043 for marine applications?
While 4043 is corrosion-resistant, it’s not the best option for marine environments. For better corrosion resistance, especially in saltwater, 5356 is the recommended choice.
What’s the difference in strength between 4043 and 5356?
5356 is stronger due to its higher magnesium content. It is ideal for applications that require high strength, such as automotive or marine welding.
Can I weld with 4043 on all aluminum alloys?
4043 is best used on alloys like 6061, 3003, and 5052. For high-strength alloys, 5356 is a better option.
Is 5356 harder to weld than 4043?
Yes, 5356 is more challenging to weld due to its higher magnesium content, but it produces stronger, more durable welds once welded properly.
Which aluminum rod should I choose for automotive repairs?
For general automotive repairs, 4043 works well. However, if you’re welding aluminum components that require strength, such as suspension parts, 5356 is the better choice.