TIG welding stainless steel is one of the most precise and rewarding welding techniques. It creates clean, high-quality welds with excellent strength and appearance. If you’re working on a small DIY project or welding stainless steel for industrial applications, understanding the process is crucial for getting strong, durable welds.
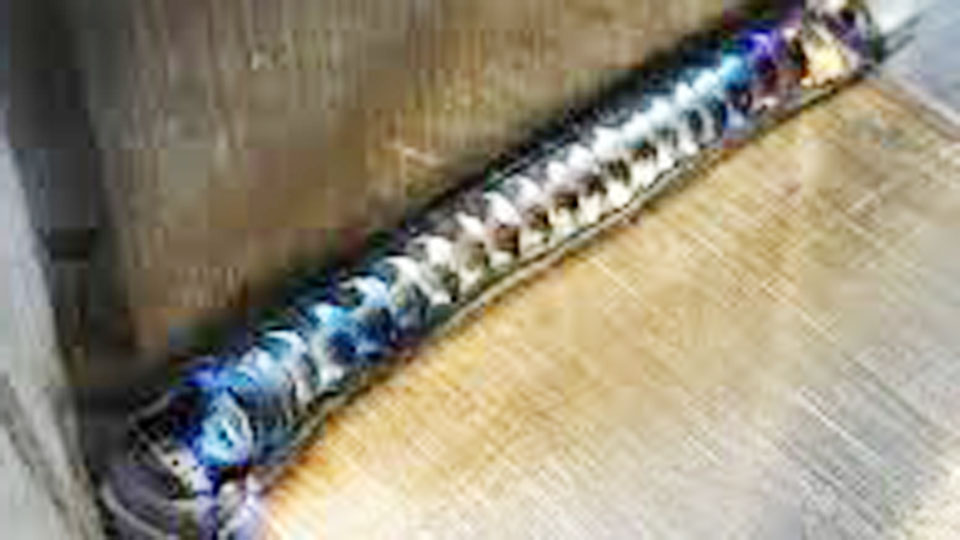
mage by reddit
I’ve spent a lot of time perfecting my TIG welding skills on stainless steel, and I can tell you that while it takes patience and practice, once you get the hang of it, the results are worth it. I’ll walk you through everything you need to know about how to TIG weld stainless steel, from choosing the right equipment to mastering the best techniques.
Why Choose TIG Welding for Stainless Steel?
Stainless steel is known for its strength, corrosion resistance, and sleek appearance. However, it can be tricky to weld because it retains heat longer than other metals and can warp if not handled properly. That’s where TIG (Tungsten Inert Gas) welding, also called GTAW (Gas Tungsten Arc Welding), comes in.
TIG welding is ideal for stainless steel because it provides precise heat control, which helps prevent warping and discoloration. It also creates cleaner welds without the need for excessive grinding or finishing. If you need strong, visually appealing welds with minimal contamination, TIG welding is the way to go.
Choosing the Right TIG Welder for Stainless Steel
Not all TIG welders are the same, so choosing the right one can make a big difference in the quality of your welds. Here are some key factors to consider:
AC/DC Capability – For stainless steel, you only need a DC (Direct Current) TIG welder since AC is mainly used for aluminum.
Amperage Range – A welder with a range of 5-200 amps is ideal for stainless steel, as it allows for fine control over thin and thick materials.
High-Frequency Start – Helps create a smooth arc without contaminating the tungsten electrode.
Pulse Control – A TIG welder with a pulse function is useful for welding thin stainless steel, as it reduces heat input and minimizes warping.
If you’re just starting, a 200-amp DC TIG welder with adjustable settings will give you plenty of flexibility.
Essential Equipment and Supplies
Before you start TIG welding stainless steel, make sure you have the right equipment. Here’s what you’ll need:
- TIG Welder – As mentioned earlier, a DC TIG welder with pulse control is ideal.
- Tungsten Electrode – Use a 2% lanthanated (blue) or 2% thoriated (red) tungsten electrode for best results.
- Shielding Gas – Pure Argon gas (at least 99.99% purity) is best for stainless steel TIG welding.
- Filler Rod – Choose the appropriate stainless steel filler rod (e.g., ER308L for 304 stainless steel).
- Welding Gloves and Protective Gear – Use high-quality welding gloves, a welding helmet with auto-darkening, and a long-sleeve jacket for safety.
- Gas Regulator and Flowmeter – To control the Argon flow rate, usually set between 10-20 CFH (cubic feet per hour).
- Stainless Steel Wire Brush – For cleaning the metal before welding.
Setting Up Your TIG Welder for Stainless Steel
Getting the right settings on your TIG welder is crucial for achieving strong, clean welds. Here are the basic settings you should use:
TIG Welding Settings for Stainless Steel
Parameter | Recommended Setting |
---|---|
Polarity | DCEN (Direct Current Electrode Negative) |
Amperage | 40-150A (depending on thickness) |
Shielding Gas | 100% Argon at 10-20 CFH |
Tungsten Type | 2% Lanthanated or 2% Thoriated |
Tungsten Size | 1/16″ for thin metal, 3/32″ for thicker metal |
Filler Rod | ER308L, ER309L, or ER316L (match base metal type) |
Gas Cup Size | #6 to #12 for better gas coverage |
Pulse Control (Optional) | 1-2 pulses per second for thin material |
If you’re welding thin stainless steel, keep the amperage lower and use pulse settings to control heat input. For thicker stainless steel, increase the amperage but maintain steady movement to avoid overheating.
How to Prepare Stainless Steel for TIG Welding
Preparation is key when welding stainless steel. Unlike carbon steel, stainless steel is more prone to contamination, which can weaken the weld.
- Clean the Surface – Use a stainless steel wire brush or an abrasive pad to remove any dirt, oxidation, or contamination. Avoid using tools that have been used on carbon steel, as they can introduce rust.
- Degrease the Metal – Wipe the welding area with acetone or alcohol to remove grease, oil, or fingerprints.
- Tack Weld the Pieces – If welding multiple sections, use small tack welds to hold the pieces together before running the final weld.
- Ensure Proper Fit-Up – Stainless steel does not fill gaps as easily as other metals, so make sure the fit is tight.
Best TIG Welding Techniques for Stainless Steel
When welding stainless steel, precision and control are the most important factors. Here are some techniques to improve your results:
Use a Short Arc Length – Keep the tungsten electrode close to the workpiece (about 1/8 inch) to maintain control.
Keep a Steady Hand – Use both hands for better stability. Some welders rest their torch hand on a stable surface to reduce movement.
Push, Don’t Pull – When TIG welding, always push the torch forward to maintain good gas coverage and avoid contamination.
Use the Right Filler Rod – Match the filler rod to the type of stainless steel you are welding. ER308L is common for 304 stainless steel, while ER316L is better for marine applications.
Control Heat Input – Stainless steel retains heat longer, so use a pulsed technique or let the workpiece cool slightly between passes.
Avoid Overheating – If the weld turns blue, purple, or brown, it means the metal is overheating. Reduce amperage or speed up your travel to prevent heat discoloration.
Common Problems and How to Fix Them
Even experienced welders run into issues when welding stainless steel. Here are some common problems and their solutions:
Problem | Cause | Solution |
---|---|---|
Warping | Too much heat input | Use pulse settings, reduce amperage, and control travel speed |
Porosity (Tiny Holes) | Contaminated surface or gas issues | Clean metal thoroughly and check gas flow |
Cracking | Wrong filler rod or improper cooling | Use the correct filler and let the weld cool gradually |
Oxidation (Blue/Gold Colors) | Poor gas coverage or excessive heat | Increase Argon flow and reduce heat input |
Post-Weld Cleanup and Finishing
After welding, remove any oxidation or discoloration using a stainless steel wire brush or a Scotch-Brite pad. If the weld has slag or contamination, use a pickling paste designed for stainless steel. This helps restore corrosion resistance and gives the weld a clean finish.
For cosmetic applications, you can polish the weld using a fine abrasive pad or a buffing wheel to blend it with the surrounding metal.
Conclusion
TIG welding stainless steel takes patience and practice, but once you get the hang of it, you’ll be able to create strong, beautiful welds. The key is to use the right settings, keep the metal clean, and control your heat input.
If you’re working on a custom exhaust, a kitchen fixture, or an industrial project, mastering TIG welding will open up new possibilities for your stainless steel work.
FAQs
What gas should I use for TIG welding stainless steel?
Use 100% Argon gas for the best results.
Why is my stainless steel weld turning blue?
This happens due to excessive heat. Lower your amperage and increase your travel speed.
Can I use a regular steel brush to clean stainless steel before welding?
No, always use a dedicated stainless steel brush to avoid contamination.
Do I need pulse settings to TIG weld stainless steel?
Pulse settings are not required but help control heat input on thin materials.
What is the best tungsten for stainless steel?
Use 2% Lanthanated (blue) or 2% Thoriated (red) tungsten for best performance.