Welding a titanium exhaust isn’t just about joining two pieces of metal; it’s about ensuring precision, maintaining the unique properties of titanium, and producing a weld that’s not only strong but visually stunning. If you’ve ever admired a titanium exhaust on a high-performance vehicle, you’ll know exactly what I mean. The welds often have a rainbow-like appearance, showcasing the care and expertise that went into the process.
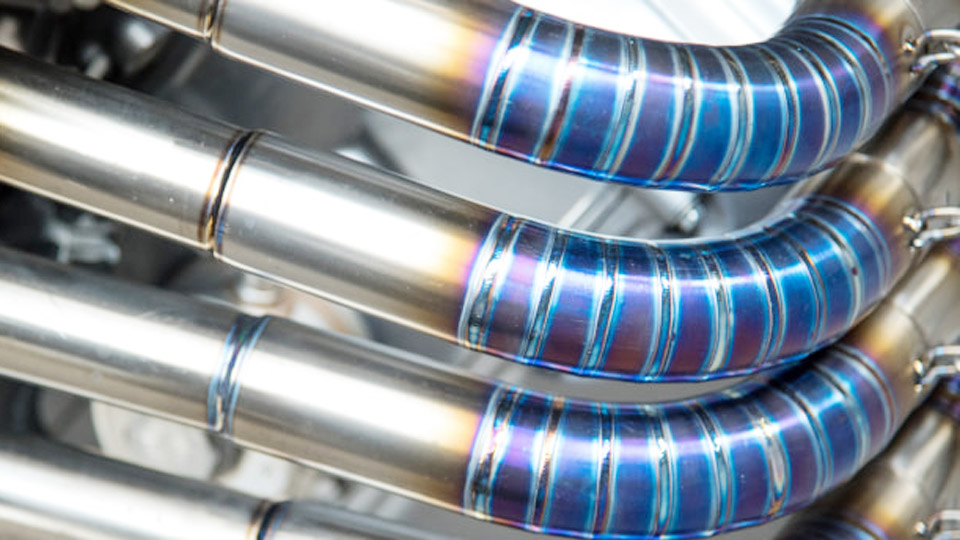
Image by onlinemetals
If you’re working on a custom car project, repairing an existing exhaust, or diving into titanium welding for the first time, this guide will walk you through every step you need to know. Let’s make it as straightforward as possible while covering all the important details.
Titanium and Its Properties
Before we dive into the actual welding process, let’s talk about titanium itself. Titanium is a lightweight, strong, and corrosion-resistant metal, which is why it’s so popular for exhaust systems, especially in high-performance and racing vehicles.
However, titanium is also sensitive to contamination during welding. Exposure to oxygen, nitrogen, or even water vapor can weaken the weld and compromise the integrity of the exhaust. This is why welding titanium requires a controlled environment and specific techniques.
Tools and Materials You’ll Need
To weld a titanium exhaust, you’ll need the right tools and materials. Using subpar equipment can lead to poor results and even damage the exhaust. Here’s a list of essentials:
Tools
- TIG Welder (GTAW): TIG welding is the best method for welding titanium due to its precision and control.
- Inert Gas Supply (Argon): High-purity argon gas is essential for shielding the weld from contamination.
- Welding Torch with Gas Lens: A gas lens ensures even gas flow, which is crucial for clean titanium welds.
- Purging Equipment: This includes purge dams or plugs to fill the inside of the exhaust with argon.
- Welding Table: A stable, clean workspace is critical.
Materials
- Titanium Filler Rods: Make sure these match the grade of titanium used in the exhaust.
- Cleaning Supplies: Acetone, lint-free cloths, and stainless steel brushes are necessary for cleaning the surface.
- Safety Gear: Welding helmet, gloves, and appropriate clothing.
Preparing the Titanium Exhaust for Welding
Preparation is half the battle when welding titanium. Without proper preparation, even the most skilled welder will struggle to achieve a good result.
Cleaning the Metal
Titanium must be absolutely clean before welding. Use acetone and lint-free cloths to remove oils, dirt, or other contaminants. After cleaning, use a dedicated stainless steel brush to remove any oxidation. Never use a brush that has been used on other metals, as this can cause contamination.
Preparing the Joint
Ensure the edges to be welded are smooth and properly fitted. A tight, even fit is crucial for a strong weld. You can use clamps or fixtures to hold the pieces in place.
Setting Up Argon Purging
Titanium requires complete shielding from oxygen, both on the weld and the backside. Use purging equipment to fill the interior of the exhaust with argon gas. This ensures the weld doesn’t oxidize from the inside.
The Welding Process
Now that everything is prepared, let’s get to the actual welding. Here’s a step-by-step guide to ensure you get it right:
Setting the TIG Welder
- Amperage: Adjust the amperage based on the thickness of the titanium. A good starting point is around 1 amp per 0.001-inch thickness.
- Gas Flow: Set the argon flow rate to about 15–20 cubic feet per hour (CFH) for the torch and slightly lower for the purging system.
- Electrode: Use a 2% thoriated or lanthanated tungsten electrode, ground to a sharp point.
Starting the Weld
- Begin with a tack weld at each end of the joint to hold the pieces together.
- Use a foot pedal to control the heat, starting with a lower amperage and gradually increasing it as needed.
Shielding the Weld
- Ensure the gas lens is delivering a consistent argon flow over the weld.
- Watch for the color of the weld. A silver or light straw color indicates proper shielding, while blue or gray suggests contamination.
Adding Filler Rod
- Feed the filler rod smoothly and steadily into the weld pool.
- Keep the filler rod tip inside the gas shield to prevent oxidation.
Maintaining the Argon Shield
- Continue the argon flow after finishing the weld to allow the titanium to cool under the gas shield. This prevents post-weld oxidation.
Troubleshooting Common Issues
Welding titanium can be tricky, even for experienced welders. Here are some common issues and how to fix them:
Contaminated Welds
- Problem: Welds turn blue, gray, or black.
- Solution: Check the argon purity and flow rate. Clean the titanium thoroughly and ensure the purge system is working correctly.
Warping
- Problem: The exhaust warps due to heat.
- Solution: Use a lower amperage and weld in short sections, allowing the metal to cool between passes.
Poor Weld Appearance
- Problem: The weld bead is uneven or unattractive.
- Solution: Practice steady torch movement and filler rod feeding. Consistency is key.
Tips for a Perfect Titanium Weld
Here are some expert tips that have helped me achieve great results:
- Practice First: Before welding the actual exhaust, practice on scrap titanium to fine-tune your settings and technique.
- Use a Large Gas Cup: A larger gas cup provides better coverage, reducing the risk of contamination.
- Monitor Gas Flow: Too much or too little argon can ruin a weld. Aim for a smooth, even flow.
- Avoid Overheating: Titanium doesn’t tolerate excessive heat well. Keep the torch moving to prevent heat buildup.
Benefits of Titanium Exhaust Welding
Welding a titanium exhaust is challenging, but the results are worth it. Here’s why:
- Lightweight: Titanium is significantly lighter than steel, improving vehicle performance.
- Corrosion Resistance: Titanium resists rust and corrosion, making it ideal for exhaust systems.
- Durability: A well-welded titanium exhaust can last for years, even under extreme conditions.
- Aesthetic Appeal: The unique colors of titanium welds add a custom, high-end look to any vehicle.
Conclusion
Welding a titanium exhaust requires patience, precision, and the right equipment, but the results can be incredibly rewarding. With proper preparation, technique, and attention to detail, you can create a strong, durable, and visually stunning weld.
I’ve worked on my fair share of titanium exhaust systems, and I can tell you there’s nothing quite like the satisfaction of seeing that perfect rainbow-like weld. If you’re new to welding titanium, don’t get discouraged. Take your time, practice, and soon you’ll be producing professional-quality results.
FAQs
Why is argon gas necessary for welding titanium?
Argon gas shields the titanium from oxygen and other contaminants, ensuring a clean, strong weld.
Can I use MIG welding for titanium exhausts?
TIG welding is preferred because it offers more precision and better shielding, which is crucial for titanium.
How do I prevent warping when welding a titanium exhaust?
Use a lower amperage, weld in short sections, and allow the metal to cool between passes.
What should I do if my weld turns blue or gray?
This indicates contamination. Check your argon flow, clean the titanium thoroughly, and ensure proper shielding.
Is welding titanium harder than welding steel?
Yes, because titanium is more sensitive to contamination and requires precise heat control. However, with practice, it becomes manageable.